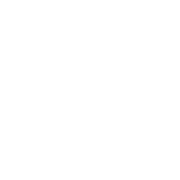 |
This month, we invite you to take a quick look through our complete Article Archive. With topics ranging from the behavior of accelerometers to proficiency in calibration, it's an excellent resource for new and seasoned measurement professionals alike. In the meantime, we appreciate your questions and are ready to step up whenever you need help with your toughest measurement challenges! |
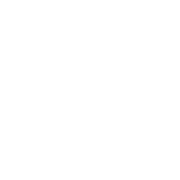 |
Filtering Dynamic Force, Pressure, and Acceleration Signals
By Pat Walter
Filters are frequency selective devices described by their types (low-pass, high-pass, band-pass, and band-reject), their characterization (e.g., names such as Bessel, Butterworth, Chebyshev), and their complexity (the filter order, which controls their rate of signal attenuation with frequency). When using force, pressure, or acceleration transducers to measure the loading to or response of structural systems, linear, low-pass filters are typically employed to condition their signals. These filters can perform any or all of the following functions
...
|
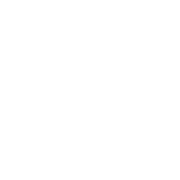 |
Tip of the Month
Plug-and-play Sensors and Calibration
Plug-and-play sensors,or Smart Transducers, typically refer to a category of sensors with calibration and/or specification information embedded or stored inside.
For example, a new generation of
digital USB piezoelectric accelerometers
has cleverly
embedded the calibration sensitivity by encoding a text string alongside the USB serial and model number descriptors. This provides calibration information using the existing USB interface, without a dedicated memory device in the sensor. Using an EEPROM memory chip is also a popular method to provide plug-and-play capability to smart transducers compliant to the IEEE 1451.4 standard. More than a decade ago, the IEEE standard introduced the concept of
TEDS (Transducer Electronic Data Sheet)
data and templates, defining the format in which sensor calibration and specification information is stored.
No matter how the sensor's plug-and-play capability is implemented, it is key that calibration information is maintained and updated each time the sensor is recalibrated. Most modern calibration systems support smart plug-and-play transducers, but it is always a good idea to obtain both digital and paper calibration certificates from the calibration service provider.
|
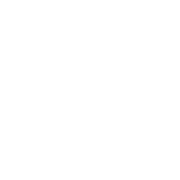 |
Blast from the Past
How High in Frequency Are Accelerometer Measurements Meaningful?
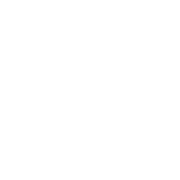 |
|
Almost all piezoelectric accelerometers in the current market place have a fundamental sensor resonance below 100 kHz. In 1983 Endevco Corporation designed a series of MEMS (Micro Electro-Mechanical Systems) accelerometers. These silicon-based piezoresistive accelerometers enabled sensor resonances of 100s of kHz to above 1 MHz. The original intent of this design (Model 7270) was to create an accelerometer with a resonant frequency high enough that it would not be excited in metal-to-metal impact or explosive environments. These types of environments are generally described by the term pyrotechnic shock (pyroshock). Unfortunately, in spite of the advantage provided by the high resonant frequencies of these accelerometers, the extremely low intrinsic damping of silicon acts as a counterbalance. The result of this low damping is often over-ranging of and damage to accelerometers when they are subjected to pyroshock. In order to support the development of a series of more robust MEMS accelerometers, this paper answers the question: How high in frequency are accelerometer measurements meaningful?
|
Thanks for joining us for another issue of
Dynamic Sensors & Calibration Tips.
As always, please speak up and
let us know what you like. We appreciate all feedback: positive, critical, or otherwise. Take care!
Sincerely,
Aaron Goosman -
Lilian Golan
- Jesse Coy
Julie Dwyer - Mike Dillon -
Patrick Timmons -
Shannon Henize
Calibration Team
|
|
|
Events
|
Seminars |
August 27-29
Portland, OR
|
May 10
Cleveland, OH
May 15-17
Buffalo, NY
June 5-6
Buffalo, NY
September 11-13
Buffalo, NY
|
Resources
|
|
|
|
|
|
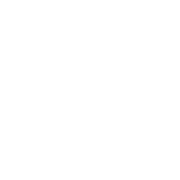 |